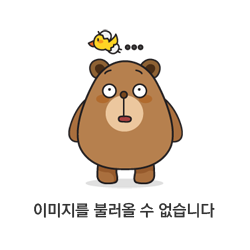
디지털 트윈, digital twin
2002년에 미국 마이클 그리브스 박사가 제품생애주기관리(PLM)의 이상적 모델로 설명하면서 등장하였다. 이 개념에 대해 NASA의 존 비커스 박사가 디지털 트윈으로 명명하고, 2010년 NASA가 우주 탐사 기술 개발 로드맵에 디지털 트윈을 반영하면서 우주 산업에서 계속 쓰여 왔다. 이후 GE가 자사의 엔진, 터빈 등 제품에 디지털 트윈 모델을 적용하면서 널리 알려져 미국 제너럴 일렉트릭(GE)가 디지털 트윈의 원조로 혼동하는 상황이 빚어지기도 했다. 컴퓨터에 현실 속 사물의 쌍둥이를 만들고, 현실에서 발생할 수 있는 상황을 컴퓨터로 시뮬레이션함으로써 결과를 미리 예측하는 기술이다. 디지털 트윈은 제조업뿐 아니라 다양한 산업·사회 문제를 해결할 수 있는 기술로 주목 받는다. 그리고 기본적으로는 다양한 물리적 시스템의 구조, 맥락, 작동을 나타내는 데이터와 정보의 조합으로, 과거와 현재의 운용 상태를 이해하고 미래를 예측할 수 있는 인터페이스라고 할 수 있다. 물리적 세계를 최적화하기 위해 사용될 수 있는 강력한 디지털 객체로서, 운용 성능과 사업 프로세스를 대폭 개선할 수 있다.
활용 영역
공장 최적화
가상 제조
센서를 활용한 자동화
원리
생명체의 환경 변화 반응 기제를 떠올리면 이해가 쉬울 수 있다. 실제로 인간의 몸은 부단히 변화하는 환경에서도 체온과 혈류(血流) 등 모든 조건을 평형 상태로 유지해야 한다. 그러기 위해 인체 표면과 내부에선 무수한 센서 세포가 끊임없이 활동 중이다. 이 세포들은 크든 작든 이상(異常)이 감지되면 다른 세포에 신호를 보내 해당 이상으로 입은 피해를 복구하고 추가 피해도 막는다. 익히 알려진 면역 기능의 작동 과정이다. 생산 공정, 혹은 이미 생산된 제품의 사용 과정에도 이와 비슷한 원리를 적용할 수 있다. 가상 목업과 비슷한 방식으로 디지털 트윈을 만들고 공정 관리자의 태블릿에 이를 제어할 수 있는 프로그램을 심은 후 생산과 소비의 전 과정에 센서를 설치해 거기서 발생하는 신호가 태블릿 속 디지털 트윈에 실시간으로 반영될 수 있도록 하는 것이다. 이렇게 되면 특정 제품(혹은 공정)의 디지털 트윈 프로그램 공유자는 언제 어디서나 제품 관련 문제 발생 여부를 실시간으로 알 수 있게 된다. 그와 거의 동시에 이들의 집단지성을 기반으로 최적의 솔루션이 도출, 현장에 곧장 전달되고 가장 적절한 조치가 취해진다. 모든 제품이 이런 방식으로 제작, 관리되면 생산 공정 오류로 인한 비용 손실을 줄일 수 있을 뿐 아니라 소비자 요구에도 한층 더 완벽에 가깝게 부응할 수 있다.
관련 기술
유한 요소법
사물 인터넷
인더스트리 4.0
Digital twin technology has moved beyond manufacturing and into the merging worlds of Internet of Things, artificial intelligence and data analytics.
As more complex “things” become connected, with the ability to produce data, having a digital equivalent gives data scientists and other IT professionals the ability to optimize deployments for peak efficiency and create other what-if scenarios.
What is a digital twin?
A digital twin is a digital representation of a physical object or system. The technology behind digital twins has expanded to include buildings, factories and even cities, and some have argued that even people and processes can have digital twins, expanding the concept even further.
The digital twin concept first arose at NASA: full-scale mockups of early space capsules, used on the ground to mirror and diagnose problems in orbit, eventually gave way to fully digital simulations.
But the term really took off after Gartner named digital twins as one of its top 10 strategic technology trends for 2017 saying that within three to five years, “billions of things will be represented by digital twins, a dynamic software model of a physical thing or system". A year later, Gartner once again named digital twins as a top trend, saying that “with an estimated 21 billion connected sensors and endpoints by 2020, digital twins will exist for billions of things in the near future."
In essence, a digital twin is a computer program that takes real-world data about a physical object or system as inputs and produces as outputs predictions or simulations of how that physical object or system will be affected by those inputs.
How does a digital twin work?
A digital twin begins its life being built by specialists, often experts in data science or applied mathematics. These developers research the physics that underlie the physical object or system being mimicked and use that data to develop a mathematical model that simulates the real-world original in digital space.
The twin is constructed so that it can receive input from sensors gathering data from a real-world counterpart. This allows the twin to simulate the physical object in real time, in the process offering insights into performance and potential problems. The twin could also be designed based on a prototype of its physical counterpart, in which case the twin can provide feedback as the product is refined; a twin could even serve as a prototype itself before any physical version is built.
The process is outlined in some detail in this post from Eniram, a company that creates digital twins of the massive container ships that carry much of world commerce – an extremely complex kind of digital twin application. However, a digital twin can be as complicated or as simple as you like, and the amount of data you use to build and update it will determine how precisely you're simulating a physical object. For instance, this tutorial outlines how to build a simple digital twin of a car, taking just a few input variables to compute mileage.
Digital twin vs. simulation
The terms simulation and digital twin are often used interchangeably, but they are different things. A simulation is designed with a CAD system or similar platform, and can be put through its simulated paces, but may not have a one-to-one analog with a real physical object. A digital twin, by contrast, is built out of input from IoT sensors on real equipment, which means it replicates a real-world system and changes with that system over time. Simulations tend to be used during the design phase of a product's lifecycle, trying to forecast how a future product will work, whereas a digital twin provides all parts of the business insight into how some product or system they're already using is working now.
Digital-twin use cases
The digital-twin examples we highlighted above – the car and the cargo vessel – provide a sense of potential use cases. Objects such as aircraft engines, trains, offshore oil platforms, and turbines can be designed and tested digitally before being physically produced. These digital twins could also be used to help with maintenance operations. For example, technicians could use a digital twin to test that a proposed fix for a piece of equipment works before applying the fix.
Digital-twin business applications are found in a number of sectors:
Manufacturing is the area where rollouts of digital twins are probably the furthest along, with factories already using digital twins to simulate their processes, as this case study from Deloitte illustrates.
Automotive digital twins are made possible because cars are already fitted with telemetry sensors, but refining the technology will become more important as more autonomous vehicles hit the road.
Healthcare is the sector that could produce digital twins of people. Band-aid sized sensors could send health information back to a digital twin used to monitor and predict a patient's well-being.
What kinds of types of digital twins are there?
IBM offers a categorization scheme based not on specific industries but on the complexity of what's being twinned. This provides a useful way to think about the needs in specific use cases and gives a look at the broad spectrum of what digital twins can do:
Component or part twins simulate the smallest example of a functioning component.
Asset twins simulate two or more components working together and let you study the interactions between them.
System or unit twins let you see how multiple systems assets work together, simulating an entire production line, for instance.
Process twins take the absolute top-level view of systems working together, letting you figure out how an entire factory might operate.
It's worth noting that adding more components to the mix adds complexity. In particular, mixing and matching components from different manufacturers can be difficult because you'd need everyone's intellectual property to play nice together within the world of your digital twin.
Digital twins and IoT
Clearly, the explosion of IoT sensors is part of what makes digital twins possible. And as IoT devices are refined, digital-twin scenarios can include smaller and less complex objects, giving additional benefits to companies.
Digital twins can be used to predict different outcomes based on variable data. This is similar to the run-the-simulation scenario often seen in science-fiction films, where a possible scenario is proven within the digital environment. With additional software and data analytics, digital twins can often optimize an IoT deployment for maximum efficiency, as well as help designers figure out where things should go or how they operate before they are physically deployed.
The more that a digital twin can duplicate the physical object, the more likely that efficiencies and other benefits can be found. For instance, in manufacturing, where highly instrumented devices are deployed, digital twins might simulate how the devices have performed over time, which could help in predicting future performance and possible failure.
Digital-twin vendors
Building a digital twin is complex, and there is as yet no standardized platform for doing so. Ian Skerrett, a consultant working in the field who has a long history in open source, has proposed the outline of a digital twin platform, though this is a first step, as suits the rather embryonic nature of the technology.
In contrast with many emerging technologies that are driven by startups, commercial digital-twin offerings are coming from some of the largest companies in the field. For instance, GE, which developed digital-twin technology internally as part of its jet-engine manufacturing process, is now offering its expertise to customers, as is Siemens, another industrial giant heavily involved in manufacturing. Not to be outdone by these factory-floor suppliers, IBM is marketing digital twins as part of its IoT push, and Microsoft is offering its own digital-twin platform under the Azure umbrella.
Digital twin vs. predictive twin
Network World contributor Deepak Puri recently outlined an example of an Oracle digital-twin tool that provides users with two options – a digital twin and a predictive twin.
The digital twin “can include a description of the devices, a 3D rendering and details on all the sensors in the device. It continuously generates sensor readings that simulate real life options.”
The predictive twin “models the future state and behavior of the device,” Puri writes. “This is based on historical data from other devices, which can simulate breakdowns and other situations that need attention.”
As part of its digital-twin initiative, Microsoft is taking the concept and applying it to processes in addition to physical products. In a whitepaper, Microsoft proposes the idea of the digital process twin:
“The Process Digital Twin is the next level of digital transformation, compounding Product Digital Twin benefits throughout the factory and supply chain,” Microsoft states. The whitepaper highlights some advanced manufacturing scenarios that product digital twins don’t support, but that process digital twins would.
Benefits and risks of digital twins
Digital twins offer a real-time look at what's happening with physical assets, which can radically alleviate maintenance burdens. Chevron is rolling out digital twin technology for its oil fields and refineries and expects to save millions of dollars in maintenance costs. And Siemens, as part of its pitch, says that using digital twins to model and prototype objects that have not been manufactured yet can reduce product defects and shorten time to market.
But keep in mind that that Gartner warns that digital twins aren't always called for, and can unnecessarily increase complexity. “[Digital twins] could be technology overkill for a particular business problem. There are also concerns about cost, security, privacy, and integration.”
Digital-twin skills
Interested in becoming a digital twin pro? The skill sets are demanding, and require specialized expertise in machine learning, artificial intelligence, predictive analytics, and other data-science capabilities. That's part of the reason why big companies are hanging out their shingle: The little guy might find it more reasonable to hire a consultant team than to upskill their in-house workers.